4 Passos Para Diagnosticar A Baixa Pressão Do Sistema
A maioria das falhas do sistema hidráulico pode ser classificada como um problema de pressão ou um problema de volume. Normalmente é fácil dizer qual delas está ocorrendo se você entende a diferença entre pressão e fluxo.
Este conceito foi abordado recentemente no meu artigo sobre Lubrificação de Máquinas intitulado “Pressão Hidráulica vs. Vazão: Entendendo a Diferença”. Tendo este conhecimento, você pode solucionar problemas de qualquer sistema simplesmente eliminando os componentes que não poderiam causar o problema, assim isolando e averiguando os possíveis responsáveis.
Em minha experiência, uma vez encontrado um defeito de pressão, o primeiro componente a ser trocado é a bomba hidráulica. Isto geralmente é um erro. Um equívoco comum é que a pressão vem da bomba, tornando-a, assim, a mais provável suspeita. Muito pelo contrário, embora seja possível que a bomba venha a ser a causa de um problema de pressão, ela certamente não é a opção mais provável. Normalmente, algum outro componente apresenta defeito. A maneira mais rápida de determinar a causa real enquanto se protege o sistema de danos posteriores é usar as quatro etapas essenciais a seguir.
Colete informações antes de tomar providências
Este passo é frequentemente ignorado com o intuito de poupar tempo, mas é muito importante na solução de problemas. Muitas informações podem ser coletadas em um curto período. A parte mais crítica da informação é o esquema do sistema. Use-o para rastrear o fluxo através do sistema e determine quais de seus componentes podem estar causando o problema. Um esquema padrão contendo componentes comuns à maioria dos sistemas é mostrado abaixo.
Você também precisará ter uma boa compreensão dos sintomas. O sistema estava funcionando bem e de repente perdeu a pressão, ou isso aconteceu gradualmente? Foi acompanhado de um ruído estranho ou de um aumento de temperatura? Caso afirmativo, de onde no sistema o som ou o calor se originou?
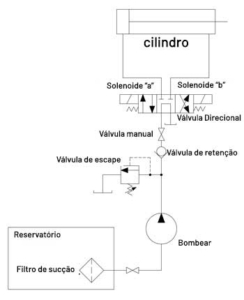
Um exemplo de um esquema típico para um sistema hidráulico
Isole a fonte de energia
Um sistema bem projetado normalmente terá alguma forma de isolar a fonte de energia do resto da máquina. Uma válvula manual é geralmente usada, mas pode ser necessário conectar um cabo. No esquema do exemplo, há uma válvula manual entre a válvula de escape do sistema e a válvula direcional. Feche-a e veja o que muda, isto é, se houver alguma mudança. Isso muitas vezes pode reduzir seu tempo de solução de problemas pela metade. Por exemplo, se a pressão for baixa e nada se mover, mas quando a válvula manual é fechada, a pressão aumenta e a válvula de escape começa a esvaziar, você sabe que a fonte de energia está funcionando bem e que o problema está em algum lugar a jusante. Da mesma forma, se nada mudar, obviamente o problema está na fonte de energia.
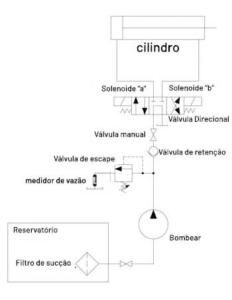
Um esquema com um medidor de vazão instalado na linha do tanque da válvula de alívio.
Verifique os itens mais fáceis primeiro
Uma vez mapeado o fluxo no esquema, identificados todos os componentes que poderiam causar um problema de pressão e isolada a fonte de energia para determinar qual parte do sistema tem o problema, comece a fazer verificações. Liste os componentes suspeitos na ordem dos mais fáceis aos mais difíceis de verificar e comece a verificação pelos itens mais fáceis. Tenho visto frequentemente pessoas cometerem o erro de ir imediatamente para o pior das hipóteses, desperdiçando horas e muito dinheiro para substituir componentes caros apenas para descobrir que não eram a causa do problema.
Em quase todas as minhas aulas sobre solução de problemas, alguém relata uma história de quando pensava ter uma grande falha de componentes de alto custo, mas eventualmente descobriu que o problema era uma válvula de retenção presa, uma válvula manual que havia sido deixada aberta, um fusível queimado ou alguma outra coisa simples que havia perdido. Pense em sua carreira. Não são geralmente as coisas simples que falham? Tente verificar os itens mais fáceis primeiro e se empenhe ao seu trabalho. Mesmo que o problema seja mesmo o grande componente, você não terá perdido muito tempo com as coisas simples.
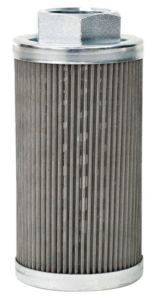
Um filtro de sucção normalmente não é verificado ou limpo com a frequência que deveria.
No exemplo anterior, vamos supor que nenhuma mudança na pressão foi observada isolando a fonte de energia, sugerindo que um dos componentes da fonte de energia estava com defeito. Neste sistema, há um filtro de sucção, uma bomba e uma válvula de escape. Qualquer um destes componentes poderia causar uma perda de pressão. está ouvindo um som agudo vindo da máquina? Em caso afirmativo, talvez a bomba esteja cavitando. A causa mais comum de cavitação é um filtro de sucção entupido. O filtro de sucção normalmente está dentro do reservatório, abaixo do nível do óleo, fora do nosso campo de visão, o que faz com que esqueçamos de sua existência e não é verificado ou limpo com a regularidade que deveria ser.
Certamente, a bomba não pode fornecer mais óleo do que pode absorver, o que pode resultar em fluxo reduzido. Às vezes, o fluxo é reduzido drasticamente. Isto geralmente ocorrerá de forma gradual com o aumento do som correspondente à velocidade reduzida, mas também pode acontecer de repente se uma grande quantidade de lodo for movida pela turbulência no reservatório. Normalmente, leva apenas alguns minutos para verificar, puxando a linha de sucção e inspecionando o filtro. Se estiver obstruído, ele pode ser limpo com ar comprimido.
Se não houver nenhum som agudo, verifique a válvula de escape. Com o sistema deadheaded, tente ajustar a válvula de escape. Se não ajustar o problema, é provável que possa estar presa. Elimine qualquer pressão residual, bloqueie o sistema e puxe a válvula. Procure no interior por sujeira, molas dobradas ou quebradas, desgaste excessivo ou qualquer coisa que possa impedi-la de encaixar-se adequadamente. Preste atenção especial aos orifícios.
Em determinado caso, a válvula de escape havia sido puxada e verificada antes da minha chegada. Disseram-me que eles tinham encontrado dois orifícios, mas ambos estavam limpos. Pedi que a puxassem novamente para que eu mesmo pudesse verificá-la antes de eliminá-la como a causa da falha. Olhei e havia um terceiro orifício que eles não tinham visto, e ele tinha um pequeno pedaço de detrito, talvez do tamanho de um grão de areia, alojado no interior. Limpamos o orifício, remontamos e reinstalamos a válvula de escape, e a pressão voltou ao normal.
A possibilidade final no fornecimento de energia é a bomba. No sistema do exemplo, é utilizada uma bomba de deslocamento fixo. A melhor maneira de verificar esta bomba é através da válvula de escape do sistema. Instale um medidor de vazão na linha do tanque da válvula de escape. Algumas vezes, isto não é possível devido à configuração da máquina. Talvez a válvula esteja acoplada diretamente ao reservatório ou montada em um coletor que esteja diretamente acoplado ao reservatório. Neste caso, instale o medidor de vazão na linha de pressão da bomba.
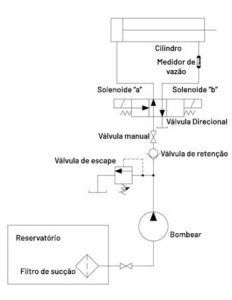
Um esquema com um medidor de vazão instalado na linha do lado da haste do cilindro.
Quando o sistema é ligado, o fluxo da bomba deve ser despejado através da válvula de escape a uma pressão muito baixa. Como não há resistência ao fluxo da bomba, ela fornecerá todo ou quase todo o seu fluxo. Aumente gradualmente o ajuste de pressão do escape da válvula. Se a bomba puder manter o fluxo com a válvula ajustada na pressão normal do sistema, está funcionando bem. Entretanto, se a vazão cair à medida que a pressão for aumentando, a bomba deve ser substituída.
Suponha que uma pressão tenha sido criada no sistema quando a válvula manual foi fechada para isolar a alimentação elétrica. Então você sabe que o problema é a jusante. O desvio através da válvula direcional ou do cilindro está causando a perda de pressão. Na maioria dos sistemas, a válvula direcional seria o componente mais fácil de verificar primeiro. Os solenóides estão funcionando? Observe a posição central do tandem. Não haverá pressão no sistema, a menos que um dos solenóides esteja energizado. Verifique se há um campo magnético com uma régua metálica ou uma pequena chave de fenda enquanto cada solenóide estiver energizado.
Uma boa maneira de testar uma válvula direcional é remover as linhas do coletor, tapar suas linhas de porta “A” e “B” e fixar uma bomba manual com um manômetro na linha de porta “P”. A porta em “T” pode ser ligada a um balde para que se possa observar qualquer óleo que passe por derivação.
No caso do exemplo, observe a posição central em tandem. Por causa do centro tandem, você só pode testar a válvula quando ela estiver em suas posições “A” e “B”. Desloque manualmente a válvula para sua posição “A”, mantendo-a deslocada enquanto opera a bomba manual. Traga a pressão para perto da pressão normal do sistema e veja se ela se mantém. Tente o mesmo com a válvula deslocada para a posição “B”. A pressão deve ser mantida por pelo menos um minuto, sem desvio para o tanque. Se a pressão cair imediatamente, a válvula é defeituosa e deve ser substituída.
Se a válvula estiver boa, teste o cilindro. Remova qualquer carga do cilindro. Isto pode exigir a desconexão da haste de qualquer movimento e pode ser demorado, que é o principal motivo para testar o cilindro deve ser o último. Estenda totalmente o cilindro, depois desligue o sistema e retire qualquer pressão, deixando o cilindro estendido. Instale um medidor de vazão na linha do lado da haste do cilindro. Ligue o sistema e aplique pressão no lado do pistão completo do cilindro. Não deve haver leitura de fluxo no medidor, e você não deve ser capaz de ver o fluido se movendo no interior.
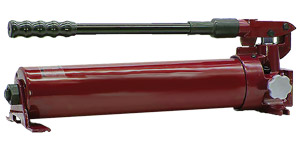
Uma bomba manual pode ser usada para testar uma válvula direcional para desvio.
Faça boas decisões
Use uma sequência lógica de solução de problemas. Muitas vezes, eu vejo o método “shotgun” de simplesmente trocar peças até que o problema desapareça. Isto é um desperdício não apenas em custos parciais, mas também em tempo de inatividade. Nunca remova um componente a menos que você tenha boas razões para acreditar que está causando prejuízo. Sempre que algo é removido do sistema, as tubulações ficam expostas a contaminantes transportados pelo ar. Contaminantes pequenos demais para serem vistos podem causar sérios danos. Embora você possa estar resolvendo um problema hoje, você pode muito bem estar adicionando mais complicações para o futuro.
Por Noria Corporation. Traduzido pela equipe técnica da Noria Brasil.
Deixe uma resposta
Want to join the discussion?Feel free to contribute!