Como a Excelência em Lubrificação Pode Tornar Sua Planta Mais Rentável e Produtiva
Existe uma crença amplamente aceita entre os vendedores e profissionais de atendimento ao cliente de que é mais fácil manter um cliente do que encontrar um novo. Dados comprovam isso, revelando que o processo de adquirir um novo cliente pode custar até 25 vezes mais do que investir o mesmo tempo e recursos na manutenção de um cliente existente.
A maioria das pesquisas mostra que um investimento muito menor na manutenção de clientes pode gerar resultados ainda maiores, com um aumento de apenas 5 por cento nos gastos com clientes existentes resultando em quase o dobro dos lucros.
Isso também é verdadeiro para as práticas de lubrificação. É muito melhor investir de forma inteligente seu tempo e recursos em equipamentos existentes do que simplesmente trocar máquinas “ruins” por novas.
A chave está na abordagem que você adota para a manutenção e operação dos equipamentos. Simplesmente jogar mais dinheiro nos problemas existentes não ajudará necessariamente. Você precisa enxergar a melhoria da vida útil da maquinaria de forma holística.
As três principais áreas de custo que a maioria das organizações considera são peças, mão de obra e tempo de inatividade. Todos orçamentam esses itens, mas no final das contas, eles são todas medidas reativas.
O verdadeiro custo só pode ser visto após os eventos de manutenção já terem ocorrido. No entanto, existem maneiras de projetar ou estimar como as mudanças feitas em seus procedimentos e equipamentos, enquanto direciona seu programa de lubrificação para a excelência, impactarão a lucratividade geral.
Conforme visto no gráfico abaixo, é possível estimar de forma conservadora que uma redução de 10 por cento na manutenção equivale a um aumento de 40 por cento nas vendas. Do ponto de vista de mão de obra/custos gerais, parece óbvio que melhorar a manutenção deve ser o objetivo desejado. De muitas maneiras, eficiência de custos e produtividade estão interligadas.
Uma máquina que funciona com mais frequência deve ser mais lucrativa, pois está alcançando seu propósito operacional desejado e não está chamando a atenção da equipe de manutenção para peças ou mão de obra adicionais. Portanto, faz sentido abordar a questão maior de melhoria de custos a partir da perspectiva de como reduzir o tempo de inatividade do equipamento, prevenindo falhas relacionadas à lubrificação.
Ernest Rabinowicz, professor do Massachusetts Institute of Technology (MIT), publicou um estudo mostrando que 70 por cento das falhas de máquinas podem ser atribuídas a problemas relacionados à lubrificação, sendo 50 por cento devido ao desgaste mecânico e 20 por cento à corrosão.
É evidente que o uso correto de óleos e graxas e a manutenção deles nas condições operacionais adequadas contribuirão muito para corrigir ou prevenir a maioria das falhas mecânicas em seu local de trabalho.
A Noria geralmente divide a jornada para a excelência em lubrificação em seis categorias: seleção de lubrificantes, recepção e armazenamento, manuseio e aplicação, controle de contaminação, análise de lubrificantes e descarte ambiental. Este artigo se concentrará nas primeiras cinco categorias e fornecerá exemplos de como melhorar em relação à excelência geral em lubrificação e eficiência de custos. Embora o descarte ambiental seja crítico, não é necessariamente um bom lugar para procurar economia de custos.
Seleção de Lubrificante
Selecionar o lubrificante adequado desde o início é o passo mais importante que você pode tomar para melhorar a produtividade das máquinas. As necessidades do seu equipamento irão guiar o processo de seleção, mas ter um entendimento abrangente das diferentes propriedades dos lubrificantes permitirá que você escolha a solução ótima.
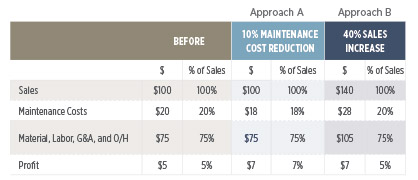
Três tipos de óleos base compõem todos os lubrificantes: mineral, sintético e vegetal. Os óleos de base sintética tendem a ter um custo inicial mais alto, mas possuem propriedades mais consistentes e, portanto, são mais estáveis. Além disso, alguns sintéticos podem ser usados em condições de planta perigosas fora das considerações específicas da máquina em questão.
Por exemplo, muitos óleos de base sintética possuem um ponto de fulgor mais alto e, portanto, são menos suscetíveis como um risco de incêndio. Se a sua planta opera em temperaturas mais elevadas (devido ao clima ou a um processo), provavelmente será benéfico mudar para um óleo sintético.
Da mesma forma, a maioria dos sintéticos possui um ponto de fluidez mais baixo e é melhor para máquinas que iniciam em condições muito frias. Novamente, os sintéticos frequentemente custam mais inicialmente, mas ao possuir melhores propriedades de fluidos e uma vida útil mais longa, eles podem se pagar em pouco tempo.
A propriedade mais importante a ser considerada ao selecionar um lubrificante é a viscosidade, e o primeiro lugar para procurar assistência ao escolher a viscosidade é o fabricante do equipamento. Mesmo que a recomendação do fabricante nem sempre seja o melhor conselho, é o melhor ponto de partida para determinar a faixa base para a máquina.
Por exemplo, um sistema de bombeamento de óleo pode ser projetado para operar em torno de 125 graus F, mas em certos momentos pode chegar a 155 graus F devido a certas condições da planta. O guia do fabricante leva em consideração apenas a temperatura normal de operação de 125 graus F em sua recomendação de viscosidade.
Para garantir que seu lubrificante permaneça viável, selecione um óleo que atenda tanto às condições mínimas quanto às máximas de operação e que tenha um índice de viscosidade (VI) que possa suportar mudanças nas condições. Se você trabalha em um clima particularmente quente ou frio, o lubrificante recomendado pelo fabricante pode estar incorreto, simplesmente porque se assume que a máquina está operando em climas mais temperados.
A temperatura é um fator importante a ser considerado, porque a vida útil do lubrificante está intimamente ligada à temperatura de operação. Reduzir a temperatura de operação do óleo em 18 graus F dobrará sua expectativa de vida.
Isso significa menos trocas de óleo, bem como menos mão de obra e tempo de inatividade. Se as temperaturas de operação do sistema não puderem ser alteradas, um resultado semelhante (mas menor) pode ser alcançado garantindo que o lubrificante selecionado tenha o aditivo de VI adequado para permitir todas as condições ambientais e climáticas.
Existem muitos outros aditivos e propriedades de fluidos a serem considerados para uma aplicação específica de máquina, mas levar em consideração a viscosidade e o VI é o meio mais eficaz de melhorar a lubrificação. Alguns fornecedores de lubrificantes podem fornecer óleo e graxa com quase qualquer pacote desejado de propriedades.
Uma maneira fácil de obter economias nesta etapa é simplificar o seu pedido geral de lubrificação. Você pode descobrir que estava comprando desnecessariamente um óleo ou graxa mais caro. Mais provavelmente, você descobrirá que a maioria das máquinas pode usar com segurança o mesmo tipo de óleo e graxa, e outra área de economia pode ser estabelecida simplesmente ao encomendar menos tipos de lubrificantes no geral. Mesmo que custe um pouco mais para ajustar os óleos e graxas encomendados, as economias serão percebidas quando o tempo de inatividade da maquinaria diminuir.
40% dos profissionais de lubrificação consideram o controle de contaminação como o fator mais importante na obtenção da excelência em lubrificação, com base em uma pesquisa recente realizada em MachineryLubrication.com, da Noria Corporation.
Recepção e Armazenamento
Após selecionar o lubrificante correto, o próximo passo é garantir que ele permaneça o lubrificante correto. Ou seja, você deseja evitar a contaminação tomando medidas para mantê-lo longe do lubrificante ou removendo contaminantes o mais cedo possível. Você dedicou tempo para escolher o lubrificante certo e aditivos, portanto, não permita que o clima, o ambiente ou manuseio inadequado prejudiquem seus óleos e graxas.
A maneira mais simples de controlar a contaminação é não permitir que ela entre em seu lubrificante desde o início. Pode-se dizer que isso é mais fácil falar do que fazer, mas manter o óleo e a graxa limpos, resfriados e secos não é tão complicado quanto alguns podem pensar.
Para evitar a contaminação, a área de armazenamento do seu lubrificante deve ser a primeira área a ser abordada. Lembre-se de que o ato de excluir um grama de sujeira ou detritos custará aproximadamente 10% do que será necessário para filtrá-lo uma vez que já esteja dentro. Não há como calcular com precisão o quanto mais caro seria se isso contribuísse para uma falha na máquina, mas é desnecessário dizer que seria consideravelmente mais alto.
Certifique-se de verificar as vedantes e tampas de todos os tambores e contêineres. Minimize a exposição do óleo ao ar e às condições climáticas armazenando lubrificantes em ambientes fechados ou pelo menos sob um telhado. Verifique se todos os sistemas de óleo estão devidamente selados. Inspecione linhas e tanques quanto a vazamentos, ferrugem ou outros sinais de falha.
Escotilhas e fechos devem estar totalmente fechados e não obstruídos por mangueiras, varetas de medição ou outros instrumentos. Sua área de armazenamento de lubrificantes também deve ser limpa regularmente. Afinal, se estiver sujo do lado de fora, é mais provável que fique sujo por dentro.
A compra de novo equipamento de armazenamento ou a melhoria do seu armazenamento existente pode não parecer uma maneira óbvia de aumentar a relação custo-eficácia do seu local. Um estudo da Universidade Monash estima que custa apenas 25 centavos por litro para deixar o óleo em um nível aceitável de limpeza (14/13/11 pela norma ISO 4406) para armazenamento ou uso inicial. No entanto, remover contaminantes do seu óleo pode aumentar significativamente a vida útil do seu equipamento.
Como visto na tabela abaixo, melhorar a limpeza do seu óleo em apenas um nível de limpeza ISO 4406 aumentará a vida útil da máquina em 35%. Quanto mais limpo fica, mais tempo a máquina não sofrerá falhas relacionadas à lubrificação. Quanto mais tempo a máquina passa sem falhar, menos tempo de inatividade, peças e mão de obra são necessários. Em outras palavras, um pequeno investimento na limpeza do seu óleo inicialmente resultará em economias enormes ao longo do tempo, apenas pela redução da taxa de falhas e do tempo de inatividade.
Manuseio e Aplicação
Intimamente relacionada ao armazenamento, a manipulação e aplicação de lubrificantes é outra área onde um pouco de precaução em suas práticas pode contribuir significativamente para a melhoria dos resultados. A chave em qualquer tarefa que envolva o transporte de lubrificantes é fazer o que for necessário para mantê-los selados e protegidos do ambiente, além de implementar procedimentos adequados.
Por exemplo, uma forma comum de contaminação é quando dois lubrificantes são misturados. Isso pode ocorrer durante o armazenamento ou aplicação, em grandes quantidades e pequenas. Diferentes óleos possuem aditivos distintos, e a mistura de lubrificantes pode fazer com que eles atuem em direções opostas.
Óleos podem ser misturados por algo tão simples quanto o uso do mesmo recipiente ou carrinho de filtro para transferência de lubrificantes. Também pode resultar de uma rotulagem inadequada de tambores e recipientes, por isso considere a implementação de um sistema único de identificação de lubrificantes (SIL) para separar e categorizar todos os lubrificantes na planta.
Ter todos os recipientes e portas marcados com etiquetas de identificação claramente visíveis e discretas ajuda a prevenir a contaminação cruzada acidental. Se nada mais, a visualização da etiqueta forçará operadores e mantenedores a observar novamente o sistema, bem como os lubrificantes e ferramentas de aplicação que trouxeram consigo.
O aumento do custo-benefício na manipulação está diretamente relacionado a não piorar as coisas. Como mencionado anteriormente, a limpeza do óleo é relativamente barata e pode ajudar a estender a vida útil do lubrificante.
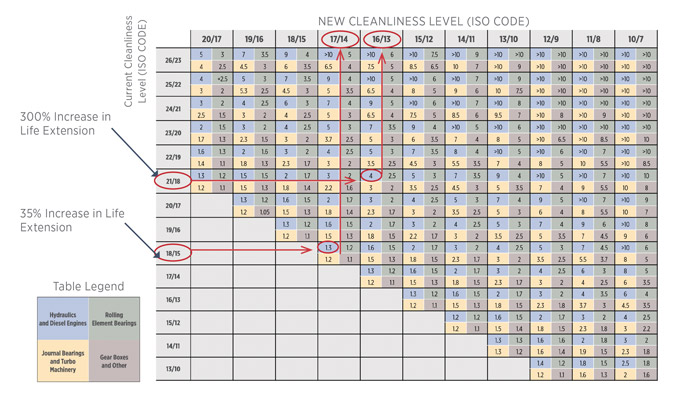
Controle de Contaminação
Na maioria dos casos, sujeira, detritos e outros contaminantes indesejados eventualmente encontrarão seu caminho até o lubrificante. Estar preparado para removê-los é a próxima melhor maneira de controlar a contaminação em seus sistemas.
Isso pode ser tão simples quanto instalar filtração em portas existentes nos tanques, motores, caixas de engrenagens e outros equipamentos lubrificados. Se esse nível de modificação das máquinas estiver fora de alcance no momento, conectar um carrinho de filtro ao seu sistema e configurá-lo para funcionar uma vez por dia ou mesmo uma vez por semana pode manter um sistema de óleo incrivelmente limpo.
Os respiros dessecantes oferecem uma maneira passiva de limpar e melhorar seu óleo. Estes podem ser instalados na maioria dos respiros do sistema com mão de obra mínima e são ótimos recursos visuais para determinar a saúde do óleo. É fácil para qualquer operador perceber quando um respiro está consumido, pois as mudanças de cor costumam ser bastante drásticas, e substituir um respiro ruim não é uma tarefa difícil.
Mudanças de equipamento mais extensas também podem ser feitas, como a instalação de filtração permanente e caminhos de amostragem. Visores, especialmente perto do ponto de enchimento, são excelentes ferramentas para visualizar o óleo sem que ele precise sair do sistema. Capas de proteção contra poeira podem ser instaladas na maioria dos encaixes de graxa, assim como pontos de purga para permitir a expulsão da graxa antiga ou ruim quando um novo lubrificante é adicionado.
Também há uma série de alarmes, medidores e outros acessórios disponíveis no mercado. O custo-benefício para você será derivado de quão bem as melhorias na máquina o alertam para uma falha relacionada ao lubrificante ou o quão eficazes elas são na prevenção ou tratamento dela. A detecção precoce lhe dá tempo para decidir como resolver o problema. Reparos programados quase sempre são mais baratos do que um trabalho urgente.
Análise de Lubrificante
Analisar o lubrificante é a maneira de determinar a eficácia do seu programa. Acompanhar contaminantes e propriedades do fluido ao longo do tempo é não apenas a melhor maneira de avaliar o desempenho do óleo, mas também o melhor indicador antecipado de falha da máquina. Por exemplo, a repentina presença de partículas de metal em uma amostra de óleo provavelmente é resultado de desgaste excessivo e indica uma falha iminente. Sem análise, pode não haver maneira de detectar essa falha antecipadamente.
A amostragem adequada está diretamente ligada à análise do lubrificante. Coletar o tamanho de amostra correto e manter a amostra o mais vedada possível é semelhante a qualquer outra tarefa de manipulação de lubrificante. Projete seu programa de análise identificando as perguntas que você deseja responder sobre seus equipamentos e sistemas de lubrificação.
Ajuste a frequência de amostragem conforme você observa melhorias ou declínios nos parâmetros. Colete amostras maiores para análises mais robustas e descobertas de causas raiz. Seu fornecedor de lubrificantes pode ter um laboratório confiável e ser capaz de analisar seu óleo a um custo razoável.
Do ponto de vista de custo-efetividade, a análise de lubrificantes oferece o feedback essencial que ajuda você a ajustar e planejar o trabalho no futuro. Um programa de lubrificação constante e previsível fornece à equipe de manutenção as informações necessárias para planejar o presente e o futuro. Um planejamento melhor é mais eficiente e permite que os recursos de mão de obra sejam considerados em qualquer dia específico.
Resultado Final
Muitas dessas recomendações podem parecer mais como custos afundados do que sugestões lucrativas. Não há muitos lucros instantâneos ou economias em implementar um sistema de rotulagem ou instalar filtros, respiros e outros equipamentos. O impacto nem sempre é imediatamente visível. Pode levar tempo para que seu sistema se ajuste a um novo equilíbrio após melhorias terem sido feitas, mas estudos consistentemente mostram que o impacto no resultado final será significativo.
Pesquisas publicadas pelo Instituto de Engenheiros Mecânicos determinaram que, para cada $1.000 investido em práticas ou melhorias adequadas de lubrificação, a economia média gerada foi de $40.000, ou um retorno sobre o investimento (ROI) de 3.900 por cento.
Estudos similares comparando práticas de lubrificação a outras tecnologias de monitoramento de condições, como termografia ou análise de vibração, descobriram que programas de monitoramento de condição de óleo e graxa valem pelo menos quatro vezes mais do que as outras opções ao longo de um período de três anos. Como discutido anteriormente, também foi demonstrado que o ROI para limpar o óleo visando a extensão da vida útil da máquina é tremendo.
Em última análise, a prova está nos resultados. Existem inúmeros exemplos de programas de lubrificação bem-sucedidos que fizeram pequenos investimentos iniciais e colheram recompensas substanciais. Coloque sua planta em um caminho rumo à excelência em lubrificação e observe como ela se torna uma das partes mais econômicas de sua organização.
Por Daniel Rader
Deixe uma resposta
Want to join the discussion?Feel free to contribute!