Monitoramento de Consumo
Nas condições atuais do mercado, a maioria das instalações está buscando maximizar o uso dos lubrificantes para evitar problemas e custos adicionais na aquisição de mais produtos. Com interrupções na cadeia de suprimentos, escassez de matérias-primas e dificuldades na obtenção de embalagens de lubrificantes, tornou-se mais importante do que nunca garantir que não haja desperdício no programa de lubrificação relacionado ao volume de lubrificantes utilizados. O tema do desperdício não é novo, especialmente quando se trata de lubrificantes, mas parece ser pouco acompanhado ou monitorado. Em termos de descarte, compras de lubrificantes e uma verificação necessária em nossos protocolos de vazamento, poucos conjuntos de dados podem ser mais impactantes.
A maioria das organizações tem uma ideia do que gastam anualmente com lubrificantes em seus orçamentos, mas poucas detalham o volume específico de cada lubrificante adquirido. Ainda menos têm uma compreensão do volume total necessário para preencher todos os compartimentos na planta. Aí reside uma das maiores oportunidades de transformar a Razão de Consumo de Óleo em um objetivo viável. A Razão de Consumo de Óleo simplesmente compara o volume total de lubrificante comprado ao volume total necessário na instalação. Este é um indicador-chave de desempenho que nos ajuda a monitorar muitos aspectos do programa de lubrificação, mas também é frequentemente utilizado como métrica para mostrar o amadurecimento de um programa.
Em sua fase inicial, um programa de lubrificação muitas vezes está repleto de tarefas desnecessárias, como excesso de lubrificação, trocas de óleo realizadas com frequência demais e vazamentos. Como pode imaginar, alguns desses problemas são mais fáceis de resolver do que outros, e alguns são mais populares para serem tratados do que outros. Não se trata apenas de decidir reduzir a frequência da troca de óleo ou lubrificar mensalmente em vez de semanalmente; é necessário fazer um trabalho extenso para amadurecer o programa e otimizar os ciclos de lubrificação. Vazamentos são mais fáceis de resolver, mas, dependendo da complexidade do sistema e dos ciclos de operação, pode ser difícil identificar e corrigir os vazamentos. Independentemente disso, podemos seguir o processo de como implementar esse KPI:
Primeiro, precisamos estabelecer uma linha de base para nossas compras atuais. Ao trabalhar com a equipe de compras, poderemos ver quanto dinheiro foi gasto em compras de lubrificantes nos últimos anos. Embora o custo seja importante de se saber, nosso objetivo é descobrir o volume total de lubrificante encomendado. Isso pode ser um processo tedioso, mas obter o volume de cada lubrificante é o primeiro passo do processo. Algumas empresas podem decidir focar apenas no volume total e não detalhar os volumes individuais de cada lubrificante, mas há benefícios em ver os detalhes. Isso ficará mais claro à medida que avançarmos no processo.
Embora não seja obrigatório, o próximo passo é determinar a quantidade de lubrificante existente nos locais de armazenamento em toda a planta. É melhor detalhar cada lubrificante individualmente. Ao examinar todas as áreas de armazenamento, você pode se surpreender com a quantidade de tambores/baldes/recipientes de lubrificante único que estão por lá. Embora o lubrificante armazenado possa parecer um estoque para uso em “emergências”, na realidade, ele representa uma responsabilidade. Com muita frequência, esses lubrificantes armazenados ultrapassam sua vida útil e podem estar contaminados a ponto de não serem adequados para uso. Além disso, uma quantidade significativa de lubrificante armazenado pode distorcer a razão de consumo, portanto, entender os níveis atuais de inventário, bem como os níveis máximos, mínimos e de reposição, é importante.
Uma vez que estabelecemos nosso histórico de volumes comprados e o volume atual armazenado, precisamos descobrir exatamente quanto de cada lubrificante é necessário para preencher completamente todas as máquinas na planta. Embora essa tarefa exija tempo e mão de obra, ela produz resultados poderosos. É comum que as plantas conheçam os detalhes de grandes reservatórios ou equipamentos críticos, mas geralmente os equipamentos menores são ignorados, e as informações simplesmente não existem no CMMS (Sistema de Gerenciamento de Manutenção Assistida por Computador). Esse processo nos permite analisar cada equipamento, determinar o volume necessário, coletar dados operacionais valiosos e, em última análise, atualizar nosso sistema de lubrificação (mesmo que seja o CMMS). Lembre-se de que, durante esse processo, você deve se concentrar apenas nos equipamentos que pretende manter. Se você tem um critério para o que é considerado “descartável”, use isso como guia. Qualquer equipamento que esteja selado ou simplesmente usado até a falha deve ser excluído dessa auditoria. Ao coletar os volumes, isso também serve como uma boa verificação das etiquetas dos equipamentos para lubrificantes, bem como dos nomes e números para garantir a consistência.
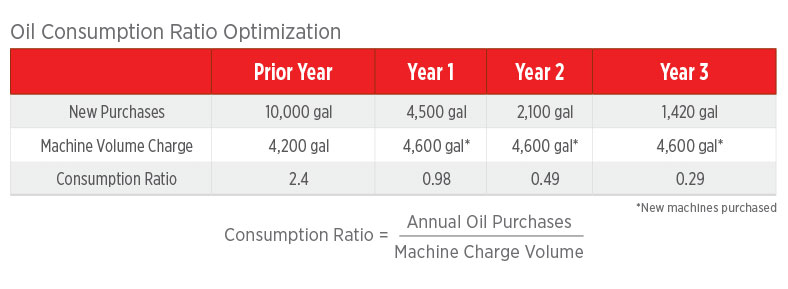
Finalmente, queremos verificar os pedidos de trabalho anteriores para determinar quantos equipamentos tiveram recentemente trocas de óleo ou recargas significativas. Talvez muitos de vocês não tenham essa informação disponível, o que é compreensível, mas é algo que vocês vão querer começar a rastrear e incluir em seus pedidos de trabalho. Isso também é algo que deve ser registrado nas rotas/rounds de inspeção. Se um operador, técnico de lubrificação ou mecânico está fazendo uma recarga, queremos saber quanto óleo foi adicionado. Isso nos permite determinar quais são os maiores consumidores em relação à nossa taxa de consumo.
Depois de concluirmos as etapas de coleta e auditoria de dados, estaremos prontos para começar a desenvolver nosso painel de Relação de Consumo de Óleo. Isso pode ser simplesmente uma planilha onde armazenamos as informações. Nos níveis mais altos, colocaremos o volume total de lubrificante comprado em relação ao volume total de lubrificante necessário na planta. Uma simples divisão do volume de compra pelo volume de máquinas nos dá a relação de consumo. No início, é comum ver uma relação acima de dois (compra de mais de duas vezes o volume de lubrificante necessário para equipar a planta), mas idealmente, devemos tentar chegar o mais próximo possível de 0,2. Para realmente aproveitar ao máximo essa métrica, você pode detalhá-la mostrando o volume total de cada lubrificante específico comprado em relação à carga da máquina para esse lubrificante, para identificar quais são os maiores consumidores e quais áreas oferecem oportunidades de melhorias.
Quando você tiver o painel construído, o foco passa para automatizar a coleta de dados (para atualizar o KPI). Embora essa seja uma métrica geralmente acompanhada anualmente, ela pode ser atualizada mensalmente para mostrar melhorias em classes de equipamentos nas quais estamos focando, como hidráulica ou caixas de engrenagens. É aqui que os pedidos de trabalho para trocas de óleo e recargas nos ajudam realmente a entender para onde todo o lubrificante está indo. Para uma visão ainda melhor do consumo, você pode comparar o volume de compra com o volume descartado; isso é um indicador de como seu programa de descarte de lubrificante pode estar funcionando.
Embora essa métrica possa parecer algo simplesmente “bom” de fazer, vocês precisam perceber que ela se concentra em mais do que apenas a quantidade de dinheiro que gastamos em lubrificantes. Quando paramos para analisar os dados, essa métrica pode servir como uma verificação necessária para muitos dos nossos processos, incluindo:
- Vazamentos – Este é talvez um dos principais vilões dessa métrica. Não apenas os vazamentos exigem mais lubrificante, mas também consomem recursos humanos. Os custos ocultos dos vazamentos não são segredo; existem custos de descarte, custos de limpeza de derramamentos e diminuição da eficiência do equipamento.
- Falhas – Uma das primeiras coisas a acontecer quando ocorre uma falha significativa no equipamento é a drenagem do óleo. Uma vez que o reparo é concluído, o óleo é reabastecido. Isso afeta a taxa de consumo, pois muitas falhas são evitáveis e, com as práticas adequadas de lubrificação, não deveriam ocorrer em primeiro lugar.
- Otimização de PM (Manutenção Preventiva) – Como mencionado anteriormente, muitas atividades são realizadas dentro de um prazo estabelecido sem qualquer fundamentação. Isso leva a uma relubrificação mais frequente do que o necessário, consumindo assim mais lubrificante do que o exigido. Concentre-se em ajustar a frequência de relubrificação com base na vida útil restante do lubrificante e na análise dos dados coletados durante a auditoria do equipamento. Você pode se surpreender ao descobrir que as máquinas que você lubrifica semanalmente ou troca o óleo anualmente poderiam aguentar de duas a cinco vezes mais tempo entre as relubrificações, mesmo em uma escala conservadora.
- Armazenamento/Rotação de Estoques – se o equipamento não estiver consumindo o lubrificante, examine as áreas de armazenamento. Isso pode revelar produtos que estão parados e não circulando rapidamente pela sala de lubrificantes, como antes pensávamos. Vistorias periódicas dessas áreas são ótimas, mas observar a proporção em que os lubrificantes estão armazenados pode ser revelador para a maioria dos responsáveis pelo programa.
- “Encolhimento” de Inventário – Embora seja extremamente difícil contabilizar cada gota de lubrificante que entra na planta, ao compararmos nosso uso com as compras e os volumes de descarte, podemos começar a descobrir onde nosso “encolhimento” de lubrificante pode estar ocorrendo. Isso pode ser resultado de vazamentos ou derramamentos que não são registrados ou complementos que não são documentados porque nossos registros de roteiros são “preenchidos de forma negligente”. Se o óleo é consumido e não descartado, isso pode indicar que nosso problema pode ser vazamento interno.
A Relação de Consumo de Óleo possui muitos benefícios em termos de dados entregáveis. Esse indicador-chave de desempenho deve ser atualizado sempre que novos equipamentos forem instalados para mantê-lo o mais preciso possível. Além disso, ele serve como um conjunto de dados útil para demonstrar como o programa de lubrificação está amadurecendo. Devemos buscar minimizar a relação de consumo ano após ano. Isso está alinhado com muitos dos objetivos de sustentabilidade e ambientais das empresas. Além disso, isso nos proporciona uma ótima plataforma para mostrar economias baseadas em valores concretos e não apenas na redução de custos. Utilize o KPI para conquistar a gestão e envolver as pessoas no investimento no programa de lubrificação.
Deixe uma resposta
Want to join the discussion?Feel free to contribute!