Por que as Trocas Programadas de Óleo não São Suficientes para Mitigar a Contaminação de Lubrificantes
Não há muitos problemas mais insidiosos ou prejudiciais para grandes máquinas industriais do que a contaminação de lubrificantes. As consequências potenciais abrangem desde problemas sutis, como aumento da temperatura de operação, até questões mais graves, como formação de espuma na máquina, falha total da máquina ou danos estruturais permanentes ao equipamento. No artigo “Abordagem Sistemática ao Controle de Contaminação”, a Vickers, Inc., descobriu que “a seleção adequada e o posicionamento de dispositivos de controle de contaminação… eliminam (a causa raiz de) até 80% das falhas de sistemas hidráulicos”.
De fato, o “Manual de Manutenção de Rolamentos” da SKF afirma que a lubrificação adequada e condições ideais poderiam teoricamente resultar em “vida infinita” para rolamentos, o que significa que os benefícios potenciais da melhoria do lubrificante são ilimitados. Além do tempo de inatividade óbvio perdido, isso também pode resultar em investigações dispendiosas de integridade do produto para testar rigorosamente todo o fluxo de trabalho.
Um fator que agrava o problema é que os primeiros sinais de contaminação do lubrificante são tão sutis e diversos que muitas vezes são negligenciados pelas equipes trabalhadoras. Mas mesmo que esses problemas nunca culminem no pior cenário, o desgaste agregado e a perda de eficiência ao longo de um período prolongado – e espalhados por uma frota de máquinas – ainda podem resultar em um impacto massivo na receita e na programação de produção.
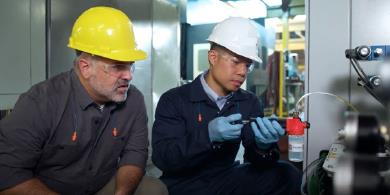
Embora as rotinas de substituição regular de lubrificantes sejam a solução padrão para esse desafio, inovações modernas tornaram possível alcançar níveis mais elevados de eficiência, confiabilidade e custo-efetividade com uma rotina de análise de óleo. Tal rotina é mais adaptável às especificidades do seu projeto e pode economizar quantidades crescentes de tempo e dinheiro ao estender o tempo de operação e reduzir os custos de manutenção ao longo de seu equipamento.
Causas de Contaminação do Lubrificante
A contaminação de lubrificantes assume muitas formas e origens distintas na indústria, tornando praticamente impossível antecipá-las todas. Algumas das fontes mais comuns incluem água, calor, ar, partículas sólidas e outros lubrificantes. Isso pode ocorrer devido às condições ambientais, procedimentos inadequados de armazenamento e manuseio, bem como erros humanos.
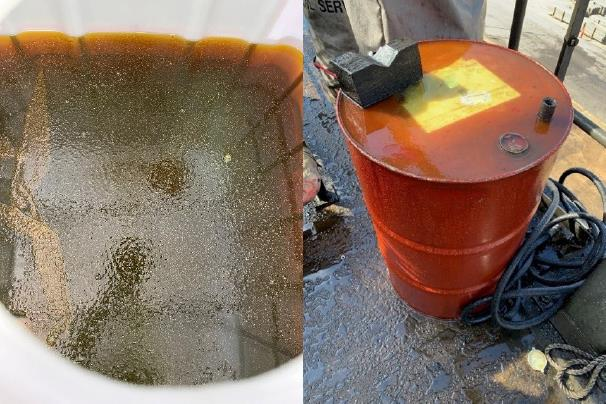
Os impactos da contaminação podem incluir:
- Temperatura – Válvula de controle de temperatura do óleo lubrificante travada.
- Aeração – O excesso de silicone de outros óleos ou aditivos de espuma de mercado pode aumentar a liberação de ar, causando falhas na bomba e outros problemas operacionais.
- Espuma pode resultar da presença excessiva de contaminantes no ar, o que pode levar a uma indicação de nível inadequada e possíveis transbordamentos do sump.
- Pressões elevadas no sistema devido a válvula de alívio de pressão emperrada.
- Restrição na sucção da bomba.
- Vazamentos devido ao desgaste excessivo de vedantes.
Uma vez identificados, esses problemas podem ser facilmente corrigidos, mas com as trocas de óleo programadas de rotina, esses problemas não serão detectados até que a empresa experimente uma vida útil mais curta do que o esperado para seus equipamentos, o que pode levar a reparos ou substituições custosos.
Desafios de Determinar se o seu Óleo Está Contaminado
A parte mais perigosa da contaminação de lubrificantes é o quão facilmente ela passa despercebida. Embora a maioria dos relatórios de análise de óleo consiga detectar o problema e alertar os usuários por meio de notificações, esses avisos costumam ser vagos e indicativos de problemas mais graves. Outros sinais, como superaquecimento, vibração excessiva e manutenção de temperaturas elevadas no reservatório, são facilmente ignorados como produtos do ambiente de trabalho.
O desgaste excessivo, principalmente em rolamentos, que pode resultar de certos tipos de contaminação, pode até ser invisível até que seja tarde demais e o dano exija manutenção não programada ou até torne a máquina inoperável.
Procedimentos Normais para Prevenir a Contaminação do Óleo
O método tradicional para prevenir a contaminação do óleo observado pela maioria das equipes industriais é um sistema agendado no qual, após um certo número de horas de operação, o óleo da máquina é drenado e os filtros apropriados são substituídos. Esse sistema geralmente prioriza máquinas críticas, passando por elas para garantir que o processo possa continuar em um ritmo apropriado. As vantagens desse sistema se devem principalmente à sua simplicidade: as equipes podem prever exatamente quando as máquinas precisarão de manutenção e agendar de acordo.
A principal desvantagem do agendamento de substituição de óleo de rotina é que ele permite que problemas de contaminação não detectados agravem o desgaste das máquinas. Isso pode potencialmente fazer com que um erro menor se transforme em um problema de manutenção caro e demorado que pode afetar os lucros e causar atrasos. Também pode introduzir um maior potencial para erros humanos, pois os sinais de alerta precoce de problemas mais graves podem ser ignorados.
Vantagens da Análise
Em contraste com as trocas preventivas de óleo em intervalos predefinidos, uma rotina de análise de óleo envolve a coleta periódica de amostras e análises do lubrificante para identificar a contaminação antes que os sintomas apareçam na máquina. Os distribuidores de lubrificantes geralmente oferecem suporte de análise juntamente com seus produtos. Embora o trabalho adicional da análise rotineira possa parecer uma ineficiência, o sistema rapidamente compensa esse trabalho por meio do aumento do tempo de atividade e da economia de dinheiro com manutenção.
Um grande motivo para isso é a realidade inevitável de erros humanos que contribuem para a contaminação do lubrificante. Não importa o quão rigorosos sejam os padrões, erros ainda podem ocorrer no armazenamento e na entrega de lubrificantes, e a pequena contaminação resultante frequentemente passa despercebida. A rotina de análise identifica esses problemas muito rapidamente, permitindo a substituição do lubrificante contaminado significativamente antes do que se fosse mantido em um cronograma simples e economizando a máquina de possíveis danos caros e demorados.
Além disso, o procedimento de análise identificará contaminantes específicos e apontará para a causa raiz – talvez contaminação por água, provavelmente devido ao armazenamento inadequado ou viscosidade incorreta do lubrificante e geralmente causada por erro humano ou procedimental – e permitirá que esse problema seja resolvido antes que cause danos duradouros ou se espalhe para outros equipamentos.
Em resumo, a análise permite uma manutenção mais preventiva e pode ajudar os gerentes a antecipar problemas antes que afetem os resultados financeiros.
Como Funciona a Análise de Óleo
Rotinas de análise de óleo são procedimentos de manutenção simples que podem ser facilmente integrados aos cronogramas de manutenção existentes.
A maneira como a análise funciona é que equipes de engenharia inspecionam sistemas críticos de equipamentos em busca de condições operacionais anormais e coletam amostras de óleo para avaliação das condições no local. Essas amostras são então enviadas para análise detalhada em laboratório.
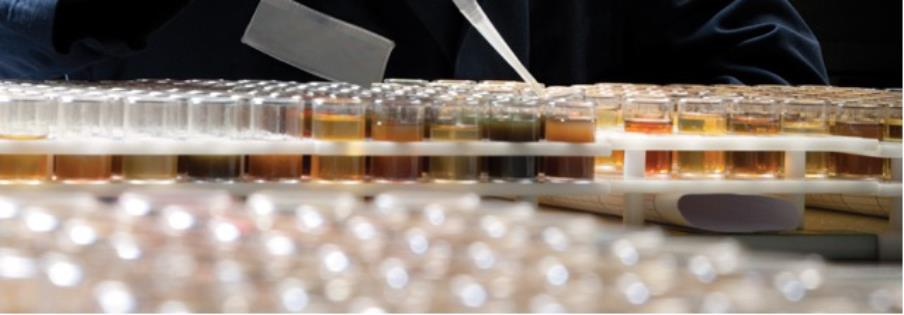
Essas verificações podem ser realizadas mensalmente em máquinas críticas (verificações trimestrais para máquinas menos críticas) com amostras enviadas ao fabricante para análise detalhada. Essa análise completa e interpretação fornece métricas sobre a eficácia e pureza do óleo, bem como informações sobre a saúde da máquina e a eficiência do projeto em questão. Isso, por sua vez, permite que o cliente obtenha uma análise de custo relativo em comparação com o cronograma de manutenção baseado no calendário que está sendo substituído.
Quando a lubrificação comercial está contaminada, os custos de manutenção aumentam rapidamente – não apenas para o próprio óleo, mas também para o tempo de inatividade prolongado e os danos ao equipamento quando as contaminações passam despercebidas. A maioria das empresas é rigorosa em relação à sua manutenção programada regular, mas está perdendo uma parte crítica do quebra-cabeça quando confia apenas em um cronograma.
A análise abrangente oferece aos gerentes uma visão mais completa da eficácia de seu programa de lubrificação, criando mais flexibilidade e eficiência ao mesmo tempo em que mantém o equipamento funcionando por mais tempo. Isso é uma parte importante de um regime de manutenção seguro e econômico para qualquer empresa.
Por Joel Scarbrough, engenheiro de lubrificação.
Deixe uma resposta
Want to join the discussion?Feel free to contribute!