Por que o óleo em seu compressor de ar é importante
Os compressores de ar são o principal componente dos sistemas de ar comprimido, que são uma parte essencial de qualquer planta industrial moderna. Após o ar ser comprimido, ele se torna uma fonte segura e abundante de energia. Por causa disso, o ar comprimido tem sido uma parte necessária dos processos industriais há décadas.
O design mais comum de compressor de ar usado em diversas indústrias hoje em dia é o compressor de parafuso. Isso ocorre porque eles são eficientes, amplamente disponíveis e estão disponíveis em uma variedade de tamanhos, desde 10 HP até 500 HP. Os designs padrão de dois estágios também podem operar em pressões de até 13 bars (188 psi).
Solucionar problemas é uma habilidade essencial para qualquer equipe encarregada de manter as máquinas em funcionamento. Nossa equipe passou anos ajudando plantas industriais a melhorar seus processos e superar desafios. Durante esse tempo, aprimoramos nossas técnicas de confiabilidade e análise de dados. Como os programas de confiabilidade atualmente dependem muito de dados e análises, compartilharei alguns números sobre o tempo de inatividade associado a uma das áreas menores dentro de uma planta: o modesto compressor de ar.
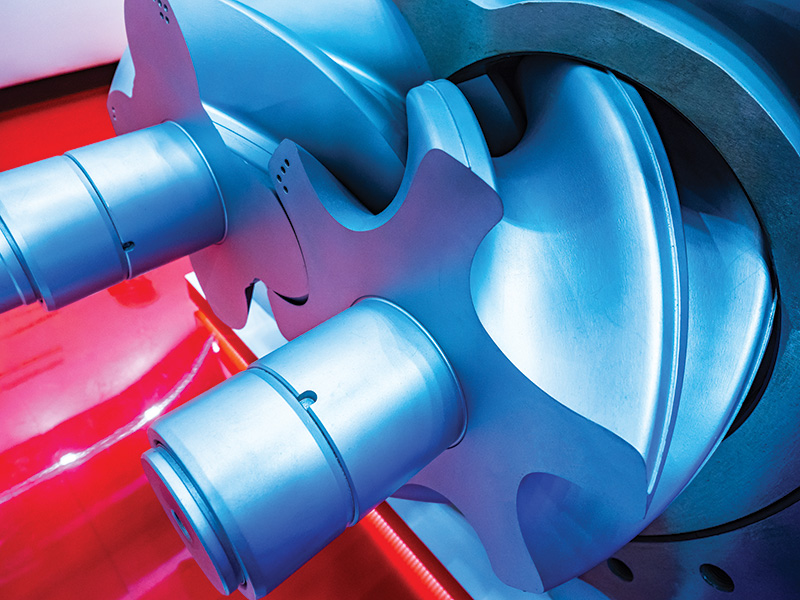
Em geral, a estação de ar comprimido geralmente representará cerca de 1,2-5% do custo total dos ativos rotativos de uma planta. No entanto, pode chegar a 20% para utilidades gerais e até 80% para indústrias como fiação e tecelagem, onde é necessário para a maioria das atividades de produção.
Embora o grau de dependência do ar comprimido varie de acordo com as indústrias individuais, a maioria delas requer ar comprimido para alguma parte de seu processo e todas sofrerão com diferentes níveis de tempo de inatividade se o ar comprimido se tornar indisponível ou se sua qualidade for comprometida. Por exemplo, de 46 a 86% do tempo de inatividade em indústrias como bens de consumo de rápido movimento (FMCG), processos de montagem, fiação e tecelagem, e siderúrgicas pode ser atribuído ao ar comprimido. Esse tempo de inatividade representa uma perda direta na produção que todos gostariam de evitar. Isso geralmente pode ser feito através do uso de redundância, mas essa estratégia tem suas limitações.
Estratégia de Manutenção de Ar Comprimido
A primeira preocupação de qualquer equipe de gestão que esteja considerando melhorias nos compressores deve ser mitigar o risco de tempo de inatividade associado ao ar comprimido. Como mencionei, a redundância é frequentemente a primeira estratégia empregada nesse caso, e muitas vezes faz sentido até certo ponto. No entanto, comprar compressores de reserva não é a única solução para o problema, nem sempre é viável financeiramente fazê-lo. Além disso, muitos fabricantes de equipamentos originais (OEMs) e equipes de serviços públicos gastam capital desnecessário ao empregar a Manutenção Preventiva nesses ativos, em vez de usar uma estratégia mais focada.
O gerente de utilidades de uma planta certa vez me perguntou quanto ele economizaria ao descobrir possíveis falhas nos compressores mais cedo. Ele estava comprando um novo compressor todos os anos, mesmo sem aumentar a capacidade de produção nem aproveitar compressores antigos.
Para responder à sua pergunta, precisamos voltar às noções básicas de manutenção adequada de compressores e mitigação de riscos de falhas. Vamos analisar um estudo de caso para entender melhor esses princípios.
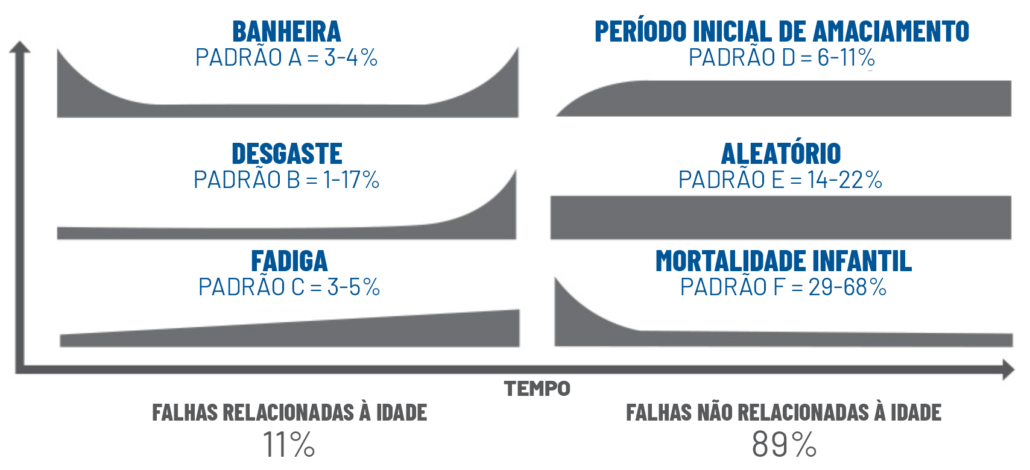
Estudo de caso
Em uma moderna usina siderúrgica atualizada, a estação de ar comprimido foi projetada com 25% de redundância para garantir a manutenção da planta, que é o tempo necessário para colocar os ativos de volta em produção. A produção poderia continuar facilmente com três dos quatro compressores, fornecendo a flexibilidade necessária para as equipes de manutenção e suporte da OEM realizarem as atividades programadas de manutenção preventiva sem afetar a produção. Tudo parecia bom e o risco foi mitigado.
Por enquanto, vamos desconsiderar o alto custo de peças de reposição e as três capacidades de armazenamento – discutiremos isso mais tarde. A principal falha desse tipo de plano de manutenção é que ele era baseado puramente em tempo e não considerava a possibilidade de falhas “aleatórias”. As falhas aleatórias geralmente não são tão aleatórias assim; ocorrem principalmente devido a erros humanos. Nos referimos a elas como aleatórias porque sua ocorrência em uma curva de padrão de falha é aleatória. Elas são a parte plana da curva que ilustra a vida útil real do ativo (no nosso caso, o compressor).
Felizmente, a usina estava realizando monitoramento de condição (CM) com a OEM para medir vibração e termografia, juntamente com análise de óleo quando necessário.
Suas técnicas e estratégia de CM foram construídas com base na Curva P-F e na capacidade das medições coletadas para ajudá-los a interceptar falhas precocemente ou em seu início. A técnica de CM mais compreendida e difundida usada na análise da Curva P-F é a vibração, enquanto a mais antiga é a análise de óleo.
A parte mais desafiadora de usar uma Curva P-F é realmente obter a curva do modo de falha correta, com base em prazos precisos entre cada estágio da falha (o eixo x é o tempo).
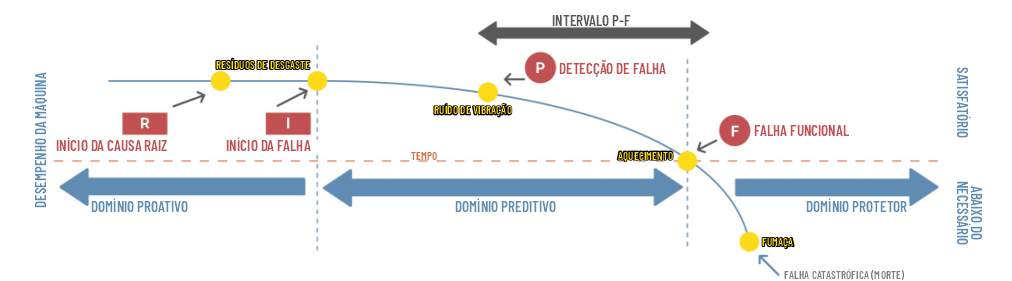
A consideração mais importante aqui é determinar como as falhas realmente ocorrem. Foi bem documentado que as falhas aleatórias representam a maioria do que vemos na indústria. Infelizmente, é comum as pessoas subestimarem a rapidez com que as falhas podem se desenvolver dadas as circunstâncias particulares.
No caso da nossa usina siderúrgica, observaremos uma falha acelerada que consumiu 68% da vida útil dos rolamentos na parte de ar de um compressor antes que alguém detectasse a possível falha. A falta de detecção desse problema resultou nos rolamentos suportando o equivalente a 16.000 horas de operação em apenas 18 dias (432 horas).
Construção do Compressor de Parafuso
Para realizar a análise de confiabilidade de qualquer equipamento, é necessário compreender o contexto operacional da máquina, como ela funciona, quais componentes têm maior risco de falha e qual modo de falha impactaria mais a confiabilidade da máquina.
A máquina na Figura 3 é um compressor de parafuso lubrificado a óleo, também conhecido como compressor de parafuso injetado a óleo. Ele possui uma parte de ar acionada por um motor elétrico e usa a pressão gerada pela parte de ar para impulsionar o óleo no circuito de lubrificação através dos componentes lubrificados, bem como dos sistemas de filtração e resfriamento.
Como você pode ver, o ar entra no sistema através de um filtro de ar, onde a maioria das partículas contaminantes destrutivas deve ser capturada. O óleo e o ar são misturados na entrada, no topo dos rolamentos, e a parte de ar começa a comprimir essa mistura. Após passar pela parte de ar, a temperatura aumenta significativamente, variando entre 73°-83°C, o que é considerado normal para esse tipo de máquina. O óleo então cai por gravidade no tanque de decantação, e o ar comprimido sai através do separador de ar e óleo, momento em que é resfriado no pós-resfriador e deixa o compressor para tratamento adicional. O óleo segue um caminho diferente, passando pelo filtro e pela válvula termostática, antes de retornar à parte de ar.
Como Destruir Rapidamente seus Rolamentos
O óleo em nossas máquinas é um ativo muito importante. Devemos garantir que ele não apenas desempenhe sua função corretamente, mas também proteja os rolamentos contra desgaste excessivo ou repentino.
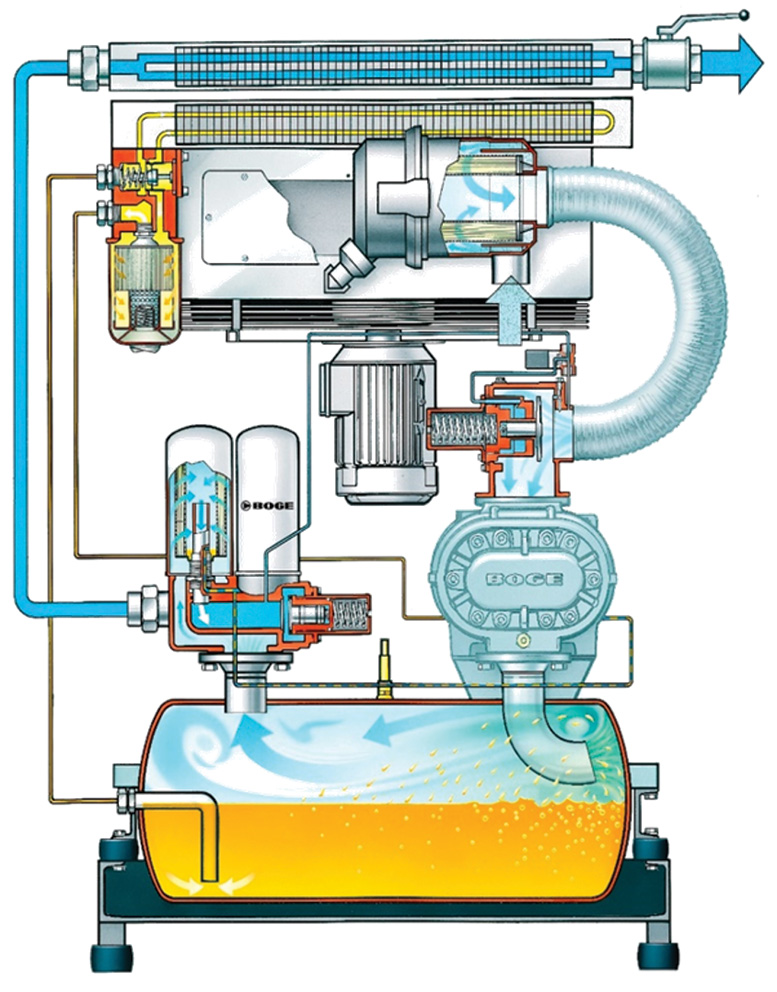
Se você observar atentamente a Figura 3, você notará uma mangueira que fornece a entrada de ar ambiente após o filtro. Esse é um ponto fraco para este compressor que pode iniciar muitas falhas se a equipe de manutenção não entender seus modos de falha ou o que procurar ao inspecionar as máquinas.
Em nosso estudo de caso, ocorreu uma pequena rachadura na mangueira de plástico após o filtro de ar devido ao desgaste do processo. Se você suspeitasse que essa rachadura era prematura, estaria correto. Uma configuração de controle incorreta havia sido implementada para manipular as pressões na mangueira. Isso foi feito para atender às solicitações das operações de evitar baixas pressões na linha de produção. A frequência com que a máquina alternava entre carga e repouso era muito rápida. Esse ciclo é contabilizado por qualquer controlador moderno de compressores, pois é uma das principais causas raiz de muitas falhas de compressores. Uma vez que essa mangueira rachou, ela apresentou uma oportunidade perfeita para que contaminantes abundantes e destrutivos, como poeira de sílica, entrassem no sistema.
Danos como esse são um convite aberto para partículas de poeira de todos os tamanhos entrarem no pior local possível, contornando o filtro e caindo diretamente nos rolamentos desprotegidos. O que aconteceu depois disso era previsível: a próxima análise de vibração indicava que os rolamentos estavam falhando.
Uma Equipe de Utilidades Desapontada
A negação é um comportamento humano típico quando recebemos notícias que não gostamos. Tentamos encontrar uma realidade alternativa que desconsidere as verdades inconvenientes com as quais fomos confrontados. Neste caso, quando a equipe de utilidades recebeu as más notícias sobre seus rolamentos, a primeira reação deles foi questionar a precisão e integridade das medições de vibração.
Ao mesmo tempo, fui solicitado a ajudar com o caso para tentar determinar o que aconteceu. Eu me perguntava como um rolamento poderia percorrer a curva P-F 37 vezes mais rápido do que o esperado. Assim que fiz uma amostra de óleo e a analisei, a resposta ficou clara. Como venho usando o método de pulso de choque há muito tempo, rapidamente notei que havia uma possível assinatura de contaminação presente no sistema. A análise do óleo confirmou minhas suspeitas e me informou exatamente quanto de contaminação havia: 37 ppm de silício (espectrometria elementar) juntamente com um código de contaminação 21/19/16 (ISO 4406). Isso já é bastante alto e, como usei espectrometria para a análise, a quantidade real de silício presente poderia ser até 4-5 vezes maior. Em combinação com uma grande quantidade de ferro também presente na análise, ficou claro que o rolamento estava se desgastando devido à contaminação.
Também determinamos que o óleo estava severamente e prematuramente oxidado. Havia alguns prováveis culpados para isso: o silício e o ferro de fato atuam como catalisadores de oxidação, mas havia outro processo em ação aqui também: o calor. O ponto de entrada da contaminação introduziu poeira de sílica diretamente no processo quente e nas folgas apertadas do compressor, concentrando drasticamente a carga. Isso, por sua vez, levou a pequenos pontos superaquecidos dentro do sistema, o que acabou levando a uma oxidação extremamente rápida do óleo.
Culpa Suficiente para Todos
Entramos na reunião com essas descobertas e comecei fazendo uma pergunta simples: Alguém inspecionou a mangueira entre o filtro de ar de entrada e o final de ar? Como já estabelecemos, eu tinha motivos para acreditar que havia rachaduras nela.
As pessoas na sala começaram a olhar umas para as outras para ver se alguém tinha feito isso. Um membro da equipe de manutenção pegou seu celular e me mostrou uma foto da rachadura na mangueira e me informou que ele havia relatado isso duas semanas antes do modo de falha ter sido indicado, mas ninguém havia tomado nenhuma providência para resolver.
Imediatamente, a equipe de planejamento contra-atacou, dizendo que ele deveria ter informado que era urgente, já que eles não tinham tempo suficiente para analisar os relatórios e e-mails… e em questão de minutos, o processo dos Quatro B começou. Se você não está familiarizado com o processo dos “Quatro B”, é um conceito bastante simples: Culpar a manutenção, Culpar as operações, Culpar o planejamento, Culpar o OEM – Culpar qualquer um.
Um dos engenheiros de utilidades tentou interromper o processo de culpar, dizendo que não estava convencido de que a poeira normal poderia causar tanto dano, o que funcionou. Todos se voltaram para mim, aguardando uma explicação. Como este é um conceito com o qual estou tão familiarizado, fiquei um pouco chocado que eles diriam isso, e esperei um momento para ver se alguém riria e diria: “só estou brincando”.
Não era uma piada. Eles estavam falando sério. Felizmente, pude explicar como essas partículas minúsculas poderiam causar tantos problemas, eles aceitaram que era possível e, eventualmente, conseguimos ter uma discussão produtiva sobre um plano de ação de mitigação de riscos.
O que podemos aprender?
Primeiro, saiba disso: O treinamento é uma necessidade. Você pode ter a melhor equipe de manutenção, mas se você não treiná-los adequadamente, eles estão destinados a falhar. Mesmo depois de treiná-los corretamente, você ainda precisa capacitá-los a fazer o trabalho por meio da preparação para inspeção (Inspeção 2.0). No caso da nossa usina siderúrgica, o membro da equipe de manutenção observou a rachadura e até tirou uma foto, mas não tinha o conhecimento para entender sua criticidade e os impactos potenciais do modo de falha que ela causou. Isso se deve, em primeiro lugar, à falta de treinamento.
A equipe de planejamento e o supervisor de manutenção também não tinham protocolos claros e organização para analisar o backlog de feedback das tarefas de manutenção preventiva que haviam sido realizadas. Implementar uma revisão sistemática das ordens de serviço concluídas garantiria que informações críticas não fossem perdidas.
Em resumo, a confiabilidade requer uma iniciativa de mudança cultural abrangente em toda a planta. Isso ajudará a garantir o envolvimento de todos na planta e permitirá que cada membro da equipe contribua efetivamente para a confiabilidade da planta.
O Plano de Mitigação
Conforme a reunião prosseguia, discutimos possíveis estratégias para mitigar riscos futuros e, mais imediatamente, estender a vida do compressor com falha o suficiente para alcançar o próximo desligamento planejado. A estratégia final incluía filtragem de profundidade de alta eficiência e um sistema de sangria e alimentação de óleo, além de monitoramento regular das condições para acompanhar o progresso da falha da máquina.
Filtrar o óleo nos deu algum tempo adicional, e adicionar óleo fresco nos ajudou a operar o compressor de ar pelas oito semanas necessárias para alcançar o desligamento planejado, momento em que revisamos a máquina e substituímos os rolamentos danificados da saída de ar.
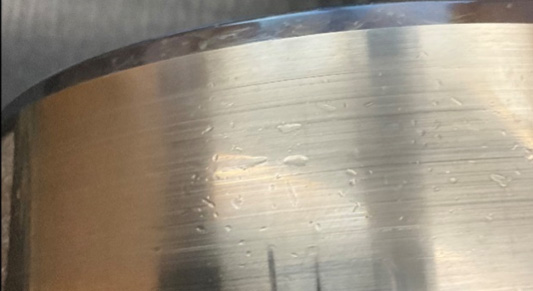
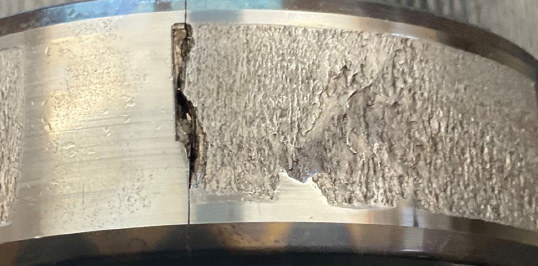
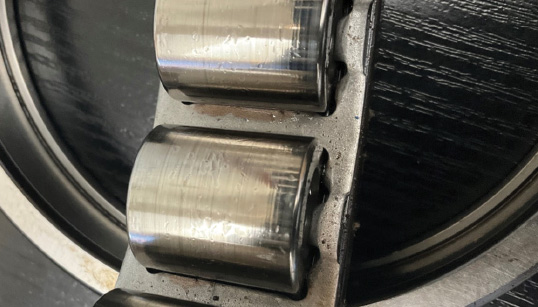
O fracasso é o melhor professor
Eu fui criado em uma família de engenheiros. Meu pai foi um dos primeiros líderes de tecnologia a começar a ensinar as pessoas sobre analisadores de vibração em 1989, no Cairo, vendendo-os e treinando seus clientes. Ele me ensinou cedo na minha vida que meus fracassos eram ainda mais importantes do que meus sucessos. Lembro-me de que, depois de voltar para casa de um teste de matemática com alguns erros, ele me disse que não importava o que eu fiz de certo. O que importava eram os erros que cometi, porque eram as coisas que eu não sabia e precisava aprender. Esses erros eram meu espaço para crescer e minha oportunidade de evoluir.
E agora?
Após um fracasso, é muito importante inspecionar as partes danificadas. Este é um passo que muitos engenheiros de confiabilidade esquecem de fazer. Pior ainda, alguns conscientemente o ignoram. As peças falhadas fornecem uma riqueza de informações sobre o que aconteceu e, se não forem examinadas, é bem provável que em breve você comece a acumular uma coleção de falhas semelhantes para exibir na prateleira do seu escritório.
As imagens acima mostram o seguinte:
- Imagem 1: As pequenas marcas de corrosão visíveis aqui são o tipo de sinais que comprovam a presença de contaminação.
- Imagem 2: A área fortemente corroída na pista interna mostra onde a contaminação desenvolveu desgastes profundos e começou a formar uma rede de fraturas. Isso eventualmente evoluiu para uma fratura completa através da peça até a pista externa.
- Imagem 3: ali estão os roletes…
O estudo de caso que examinamos nos permite tirar várias conclusões.
Desde o início, estabelecemos a importância de projetar seu programa de manutenção com base em dados confiáveis de confiabilidade. Também aprendemos que a monitoração de condição (CM) é uma das melhores ferramentas que podemos usar ao buscar uma gestão eficaz de ativos. Ter uma compreensão precisa e oportuna da operação da máquina e de seus modos de falha é a melhor maneira de determinar a combinação correta de atividades (PM, CBM, tarefas de inspeção, etc.) que se adequa ao ápice da curva P-F e nos ajuda a alcançar uma extensão tangível da vida útil da máquina.
Acima de tudo, aprendemos que o treinamento adequado é o investimento mais importante que podemos fazer em nossa equipe. O treinamento estimula observações e decisões fundamentadas, além de promover as mudanças culturais necessárias para capacitar o trabalho de suas equipes na planta. O treinamento é o paraquedas dourado de sua planta, dando-lhe a capacidade de planejar e contornar falhas custosas que costumavam ser apenas suportadas.
Em resumo, uma equipe bem educada, capacitada e organizada, com uma cultura de confiabilidade adequada, economizará muitos custos desnecessários.
Deixe uma resposta
Want to join the discussion?Feel free to contribute!