Você está pronto? Problemas na cadeia de suprimentos despertam a necessidade de lubrificantes de backup.
Nos últimos anos, a Noria recebeu uma série de solicitações de grandes usuários que precisavam de lubrificantes de backup para aplicações críticas. Disrupções no fornecimento de lubrificantes têm sido o principal motivo dessas consultas. Ao conversarmos com muitos contatos da indústria, descobrimos que o problema é generalizado. Uma escassez de estoque de aditivos parece ser o principal culpado, mas em outros casos, problemas na cadeia de suprimentos de óleo básico foram responsáveis. Alguns usuários têm tentado implantar soluções paliativas para reduzir o consumo de óleo. Isso inclui a extensão dos intervalos de troca de óleo e a realização de complementos, em vez de mudanças de óleo completas. Claro, uma maneira de fazer com que o óleo dure mais é reduzindo a degradação de aditivos e óleo básico usando a estratégia de limpeza/seco/resfriado. Em outros casos, aditivos suplementares podem ser reconstituídos no lubrificante envelhecido – algo como um impulsionador. No entanto, isso pressupõe que esses aditivos possam estar disponíveis. Também pode ser prudente manter reservas maiores à mão, eliminando a gestão de estoque just-in-time até que os suprimentos confiáveis retornem. Note que o armazenamento prolongado de lubrificantes também pode apresentar problemas agudos. Faça sua lição de casa sobre questões de estabilidade de armazenamento a partir de artigos anteriores encontrados aqui no blog da Noria Brasil. No entanto, essas estratégias podem ser nada mais do que uma solução temporária para problemas crônicos futuros. Mudar para um fornecimento de lubrificante mais confiável pode ser sua melhor aposta. No mínimo, você precisa estar “pronto” com um lubrificante de backup que possa ser imediatamente implantado em seus equipamentos de planta quando necessário. Não espere até estar na última gota; pense nos cenários mais pessimistas e nos planos de contingência ou remédios que você tem à disposição.
Riscos de uma mudança abrupta para um lubrificante de backup
Se uma mudança de lubrificante for possível (ou, por qualquer motivo, inevitável), é melhor ter uma compreensão clara dos riscos potenciais. Sua melhor opção pode não ser tão boa quanto parece. A verificação é absolutamente necessária. Felizmente, a indústria tem considerável experiência e compreende os riscos associados a uma mudança repentina para um lubrificante de backup. Estes incluem: O lubrificante de backup era incompatível com o lubrificante anterior, e alguma mistura era inevitável (ou não foi devidamente evitada). A incompatibilidade resultou em defeitos de desempenho do lubrificante e consequências de confiabilidade associadas. O lubrificante de backup era incompatível com sedimentos internos, lodo e/ou verniz. O lubrificante de backup era incompatível com as superfícies internas da máquina (pintura, tratamentos de superfície, filtros, elastômeros, calafetagem, adesivos, etc.). Alguns aditivos agressivos de lubrificante podem lixiviar metais sensíveis (estanho ou cobre, por exemplo). O lubrificante de backup era incompatível com as condições de operação e exposições (extremos de temperatura, contaminantes, gases, produtos químicos de processo, sprays de lavagem, refrigerantes, etc.). O lubrificante de backup tinha fraquezas de desempenho ou desvantagens que o lubrificante anterior não possuía. Embora algumas características do novo lubrificante possam ser superiores ao lubrificante anterior, muitas outras podem exibir desempenho abaixo do padrão.
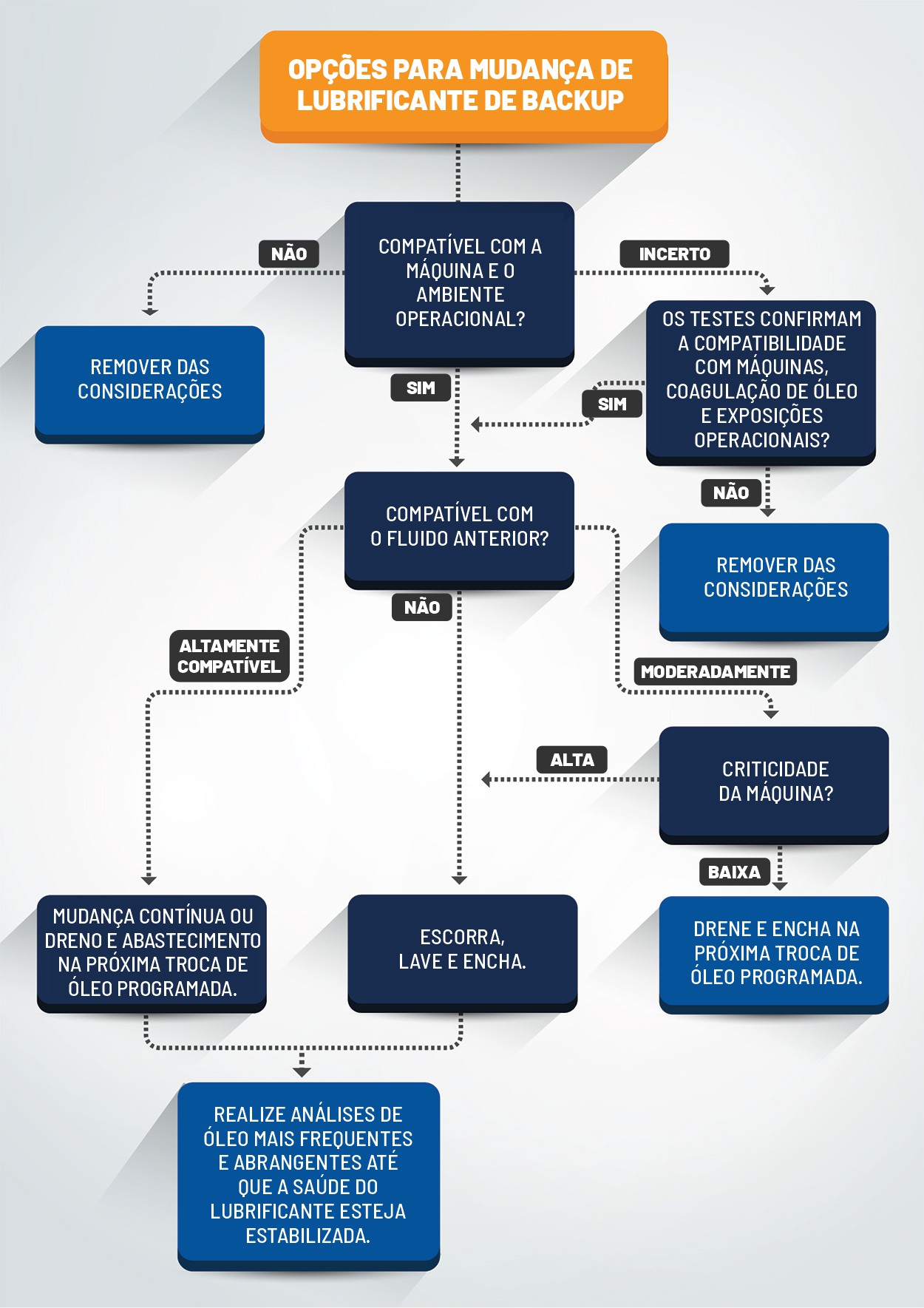
Figura 1. Os riscos mais elevados de mudanças de lubrificante de backup estão associados a: Equipamentos antigos (serviço prolongado com o lubrificante anterior) Química de aditivos desconhecida e testes limitados de compatibilidade realizados Alta carga de trabalho da máquina e criticidade Formulações de lubrificantes complexas
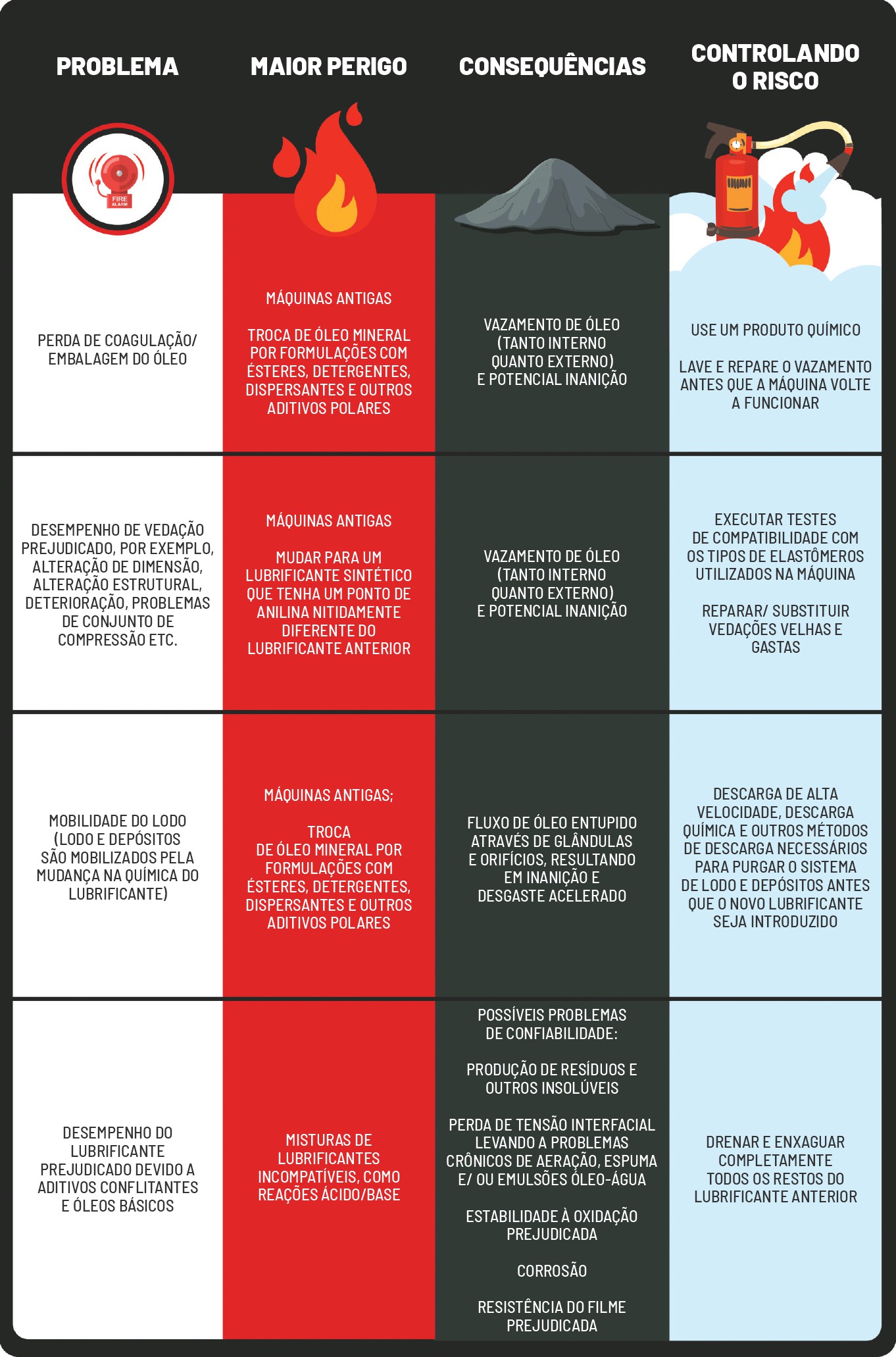
Figura 2.
Verificar a compatibilidade com antecedência
Existem inúmeras normas da indústria que fornecem orientação sobre testes de compatibilidade (ASTM, FTC, etc.). O protocolo típico para óleo (por exemplo, ASTM D7155) envolve a preparação de misturas binárias dos lubrificantes com questionável compatibilidade. Misturas como 50:50, 95:5 e 5:95 são frequentemente usadas, mas isso pode ser modificado para melhor se adequar à aplicação alvo. De acordo com a ASTM D7155, as misturas devem passar por um curto tempo de amaciamento a uma temperatura elevada. Isso permite que o óleo base e os aditivos interajam quimicamente e fisicamente, após o qual as misturas estão prontas para serem inspecionadas e testadas mais a fundo. Se a mistura apresentar flocos, sedimentos, turvação ou descoloração, os lubrificantes são confirmados como incompatíveis (teste de nível um) sem necessidade de análise adicional. Se isso não ocorrer, uma sequência de testes adicionais será necessária. Os testes exatos e as condições de aprovação associadas a esses níveis suplementares devem ser cuidadosamente pensados (dependendo do lubrificante, aplicação e exposição). A criticidade da máquina desempenha um papel vital nessa decisão, juntamente com outros fatores. Uma especificação do lubrificante pode ser usada como base para os testes suplementares, ou o desempenho listado no novo lubrificante em sua ficha técnica pode ser usado. No entanto, uma especificação bem construída é necessária para aplicações críticas. Exemplos de testes de desempenho podem incluir filtrabilidade, capacidade de lidar com ar, capacidade de lidar com água, resistência do filme, estabilidade à oxidação, supressão da corrosão, etc. A seleção de testes para os níveis suplementares é amplamente determinada pelas necessidades de vida útil de serviço (do óleo) e as necessidades críticas de desempenho na aplicação da máquina alvo. Novamente, métodos de teste padronizados podem ser empregados, especialmente em relação a elastômeros e tratamentos de superfície. Os riscos relacionados a exposições químicas podem incluir certos gases (refrigerantes, amônia, sulfeto de hidrogênio, etc.), combustível, refrigerantes, produtos químicos de processo, etc. Testes padronizados personalizados ou modificados também podem precisar ser realizados para avaliar sua compatibilidade.
Desenvolvendo uma Estratégia de Troca de Óleo e Flushing
Por razões óbvias, uma troca é fortemente desencorajada se for encontrada incompatibilidade (ou incerteza) entre o novo lubrificante de backup e a máquina (selos, por exemplo) ou o ambiente operacional (por exemplo, gases de processo) (veja a Figura 1). Se uma troca ainda for inevitável, procure outras opções de lubrificante para mitigar os riscos e consequências. Não subestime a importância disso. Se a incompatibilidade for encontrada apenas entre as misturas de lubrificantes (não na máquina ou exposições operacionais), uma troca geralmente pode ser realizada com sucesso. No entanto, isso requer precauções especiais, como a remoção completa do lubrificante anterior e a descontaminação de sedimentos, lodo e verniz. Quanto maior o perigo, mais rigoroso deve ser o procedimento de drenagem e flushing. Podemos relacionar isso à definição de risco, que é a probabilidade de um problema de compatibilidade multiplicado pelas consequências da incompatibilidade. A alta incompatibilidade de lubrificante (determinada por testes) está relacionada à probabilidade de ocorrência de um problema, e a alta criticidade da máquina define as consequências da falha (lubrificante e/ou máquina). A criticidade inclui coisas como o custo de reparo, perda de produção, custo de flushing e riscos de segurança. Quando o perigo é maior, drene completamente o sistema de todos os resquícios do fluido anterior. Procure por cavidades de fluido aprisionado em aquecedores, resfriadores, loops off-line, mangueiras, filtros, armadilhas de baixo ponto, extensões de linha, etc. Mesmo após a drenagem completa, o óleo ainda ocupa as superfícies internas da máquina. Essas superfícies molhadas, juntamente com a presença de lodo e depósitos de superfície (incluindo verniz), apresentam alto risco. Siga a drenagem com um fluido de deslocamento ou chase para remover o óleo anterior restante. O fluido de deslocamento é sacrificial e, como tal, precisa ser completamente compatível com a carga final de fluido e relativamente barato. Um óleo de base de baixa viscosidade às vezes é usado, ou talvez até um óleo de transformador. Aquecer o fluido de deslocamento e passá-lo por todas as zonas de fluido internas com alta velocidade (número de Reynolds alto) dá os melhores resultados. Muitas empresas independentes oferecem serviços de flushing que valem a pena considerar.
Maiores perigos na troca de óleo
Se as superfícies da máquina não forem limpas completamente, pode ser necessário fazer uma lavagem química. Isso pode ser adicionado ao fluido de deslocamento em uma concentração de 5% a 10%. Um produto comum vendido pela DuBois Chemicals é o limpador Step-One (também disponível de outras fornecedoras de lubrificantes). Ele não é um solvente, mas um produto detergente de sulfonato de cálcio misturado em um óleo mineral de base que se mostrou muito eficaz. Uma desvantagem é que este limpador deve ser completamente removido do sistema antes que o lubrificante final seja introduzido. Isso é normalmente feito com mais um fluido de deslocamento.
Monitoramento rigoroso pós-troca de óleo
Após a lavagem química ter sido concluída e a carga final de óleo adicionada, combata a lei das consequências não intencionais usando uma estratégia de monitoramento pós-troca de óleo. Acelere a análise do óleo e outras inspeções da máquina (espuma, vidros turvos, alta temperatura, descoloração, operação ruidosa, etc.) – teste a tendência de formação de espuma e as características de desemulsificação. Além disso, não se esqueça de mudar os procedimentos de lubrificação para incluir o novo lubrificante para completar e trocas de óleo. Certifique-se de rotular corretamente a máquina com o novo lubrificante também.
Deixe uma resposta
Want to join the discussion?Feel free to contribute!